Posted by
Dennis Ofiara | From the Field
TBMs have
become well accepted in civil construction tunneling and excavate a high
percentage of civil construction projects each year. But each year in the
mining industry, far more kilometers of tunnels are excavated for mining
purposes than for civil purposes. The amount of tunnels needed for mining
operations is staggering.
Some
examples from metal mines:
- A large, deep gold mine has
over 800 km of tunnels. That is a single mine!
- One small underground metal
mine excavates over 13 km of tunnel each year
- In the Sudbury, Ontario mining
district, there are over 5000 km of mine tunnels
If tunnels
for coal mining were included, the statistics would be even more dramatic. But
all these tunnels hold a little-known secret.
The Lack
of Mechanized Tunneling
How many of
the above thousands of kilometers of mine tunnels do you think have been
excavated by TBM? The answer is “Nada”. Compare that to the thousands of
kilometers of civil construction tunnels built over the last decades, which
required hundreds of TBMs. Why such a great disparity when the objective in
both industries is to excavate underground openings as rapidly, economically,
and as safely as possible? What are the differences in these industries?
In TBM
civil construction, the TBM crew members that know how to make things happen
underground, that know how to drive the machines, how to lift heavy components
and repair the equipment, how to get the trains in and out to remove the muck
and to bring in supplies, are known by a special name. They are known as the
“miners”. Yet the only thing they are mining is the muck, no coal, no minerals.
But “miners” is a term of reverence for someone who knows how to excavate a
tunnel rapidly and efficiently. When a civil tunnel is progressing well, they
say “now we’re mining”. (Well, sometimes they also say this sarcastically
sometimes when things are going poorly underground.) Why aren’t such talented
miners, who know how to make a TBM perform, using their TBMs to excavate
thousands of kilometers of mine tunnels each year? What are the differences
between civil tunneling and mine tunneling?
TBMs for
Civil Tunnels
TBMs have
become well accepted for civil tunneling. TBMs designs have become widely
adapted for different ground conditions or specialized applications: Hard rock,
soft ground, mixed face, pressurized face. Various types of ground support can
be installed, according to current geological conditions. More current “hybrid”
or “Crossover” TBM designs can handle widely different geological conditions,
with the TBM adaptable to cope as conditions change.
Civil
tunnels are generally long tunnels, where the efficiency of TBM excavation
offsets the longer mobilization and demobilization times. And civil tunnels are
generally designed with equipment mobilization/demobilization in mind. Suitable
sized shafts are located to allow relatively simple introduction or retrieval of
the TBM equipment.
The most efficient type of TBM is
the full face, rotary type TBM, which produces a circular tunnel profile. The
circular profile is nearly universally accepted for civil construction. It is
the optimum profile for fluid flow for fresh water, waste water, or hydro
tunnels. It is also widely accepted for vehicular civil tunnels that need a
flat roadbed. A flat roadway is constructed within the circular tunnel profile
and the remainder of the profile within the circle is used for ventilation,
services, escapeways, etc.
Some
efforts have been made to develop non-circular profile TBMs for the civil
sector. These machines include the Mini-Fullfacer, the Mobile Miner, and
horseshoe shaped shields with excavator boom or roadheader. Such machines may
produce a non-circular profile that is better for that specific job. But
usually, there is a penalty in production rate compared to full face, circular
TBMs.
TBMs for
Mine Tunnels
There have
been some notable successes to the application of circular profile “civil type”
TBMs for mining projects. Benefits have been lower costs, quicker access, and
improved safety. Some examples include:
However,
application of TBMs for mine tunnel construction has remained surprisingly
limited. Why is this? Tunnels for mining are often not so long, or a
developed in shorter phases, with the excavation front moved from place to
place within the mine. TBMs and their constituent components are large and
heavy. It is not easy to mobilize a TBM deep underground in a mine at a remote
face. Better efforts must be made to make TBM transport and mobilization within
the mine practical. This includes considerations for steep ramp roads and other
restricted cross sections within the mine.
Efficient
TBMs are highly productive, but require a lot of power, ventilation, cooling,
and support services. These need to be part of the mining plan so that the TBM
has the necessary support and can provide the full benefit. Operating personnel
with proper skills are also essential. If a TBM is introduced into a mining
environment, either the mine personnel need proper TBM training or motivation,
or the TBM drive must be isolated as a “stand alone” operation within the mine
and be given proper priority of skilled personnel and the necessary services so
the full benefit can be realized.
Mines often
do not accept the circular profile produced by the most efficient, full face
rotary TBMs. Mine tunnels are usually designed with a flat invert to allow for
passage of rubber tired vehicles during the production phase of the mine
tunnel. Many efforts have been made to provide TBM type equipment that produces
a flat invert. Some have been relatively successful. But generally these
machines do not provide the same productivity of efficient, full face circular
profile TBMs. Rail bound mining vehicles can be used in the circular tunnel to
take advantage of this TBM efficiency. Or, precast invert slabs, poured in
place concrete, or partial invert filling can be used in a circular tunnel to
provide a flat roadway. The cost/benefits must be analyzed and presented to the
industry for a change to occur.
Mining
plans often have tunnels with steep gradients and sharp radius curves. On steep
gradients (up to 12-15 degrees), the most efficient haulage is usually by belt
conveyor. However, the belt system is not effective if there are sharp radius
curves. And typical TBM curve ability is limited. Special TBM designs can be
made that allow for excavation in sharp curves, but there is a compromise in
reduced TBM performance.
Mines
need Versatile TBMs
It seems
the mining industry needs the benefits that TBMs can provide. Open pit mines
are becoming depleted, and mining activities are reaching deeper. Longer access
tunnels are needed. Safety and speed of development are paramount. TBMs can
offer these advantages, but have limitations. Special TBMs can be developed
that meet special requirements, but usually there is a penalty in reduced TBM
performance. The mine planners and the TBM equipment designers must work
together at an early stage in the mine planning to determine the optimum
compromise between most desirable mine plan, and most beneficial application of
TBM equipment. A good partnering approach is necessary in the planning stage,
as well as the operating stage, to allow for the most efficient application of
TBM equipment to the needs of the mine.
By Dennis
Ofiara, Chief Engineer
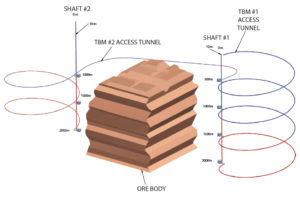
If you would like to read more of Dennis Ofiaras’ blogs
please visit http://www.therobbinscompany.com/blog/2017/06/05/tbm-equipment-mining-industry/