3 Ways to Bore More Efficiently in Extremely Hard Rock: Maximize your TBM Advance through Minimized Downtime
When the rock seems unbreakable, stresses are multiplied: The cutters must be stronger, the TBM more durable, and the operation optimized to keep equipment running smoothly. Once rock hardness rises beyond 180 to 200 MPa UCS, the limits of cutting tools are put to the test.
Given the clear risks of excavating massive, hard rock, how can tunnellers set themselves up for the best possible chance of success? The combination of knowledgeable personnel, properly designed equipment, and rigorous TBM operation and maintenance are making excavation of hard rock—even extremely hard rock strengths of 300 MPa UCS or more—possible.
1: Consider your Cutting Tools
Cutters are a significant factor for efficient excavation when rock is extremely hard. To that end, Robbins has developed Extra Heavy Duty (XHD) rings for projects where Heavy Duty (HD) rings are close to their design limit in terms of the thrust force required to break the rock. The XHD rings resist chipping, mushrooming, and other damage that can occur in very hard rock conditions. Enhanced heat treatment gives the discs increased hardness and strength without the normally-associated reduction in fracture toughness.
The rings have a proven track record: they’ve been put to the test at several jobsites, including Norway’s Røssåga headrace tunnel bored in rock from 200 to 280 MPa UCS. Initially, HD cutters mounted on the Main Beam TBM’s cutterhead experienced low cutter life in the range of 100 to 150 cubic meters bored per cutter. XHD rings were gradually introduced onto the cutterhead to determine what, if any improvement in cutter life could be obtained. It is likely that the performance in the very hard sections was improved by a minimum of 25%. The benefits of the XHD are also likely to explain the superior cutter life for the remainder of the project, even in the relatively softer ground.
2: Optimize Penetration Rate
Harder rock requires equipment that can stand up to high stresses. Penetration rate and thrust are exponential functions. The first rule is: Push as hard as you can. The more thrust the better. A machine with a robust steel structure is needed to take the higher loads without damage.
But penetration rate is trickier: The overall goal in hard rock should be to operate TBMs as efficiently as possible to maximize production. This means increasing penetration per revolution as much as possible. Consumption of cutterhead wear parts is related to the number of revolutions of the cutterhead, so it follows that increased penetration per revolution will result in fewer total revolutions of the cutterhead, reduced consumption of wear parts and fewer cutter changes for the duration of the tunnel.
The TBM Operator should therefore be looking for the best advance at the lowest RPM, because lower RPM reduces wear on the outer cutters and periphery of the cutterhead. Robbins has conducted site tests at multiple sites over several years showing that a lower RPM achieves the same and often better penetration rates than a higher RPM in hard rock. This can be clearly seen in the data: For example, on an 8 m diameter cutterhead, the circumference is 25.12 m. At 10 RPM during TBM operation, this would mean 251.2 m of travel in one minute. If the speed is reduced to 8 RPM, the distance would be 200.9 m of rotation—a full 50 m less in one minute. That is 3000 m less per hour, reducing wear substantially.
Malaysia’s Pahang Selangor Water Tunnel was a good example of this phenomenon. What is now the longest tunnel in Southeast Asia, at 44.6 km, required excavation using three 5.2 m diameter Main Beam TBMs mounted with 19-inch disc cutters. The machines operated in abrasive granitic rock exceeding 200 MPa UCS, up to 1,200 m below the Titiwangsa Mountain Range. RPM trials were conducted on the three TBMs, showing that an increase in penetration rate per revolution of 15 to 20 percent could be achieved by decreasing the RPM from between 11.5 and 12 to just 9.5. While the overall advance rate was lower because of fewer revolutions, downtime was decreased and cutter changes were reduced by as much as 19%. The overall time savings more than made up for the decreased advance rate.
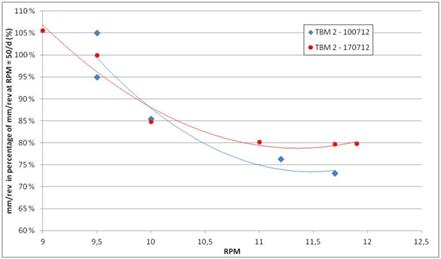
In site tests, reduced RPM resulted in increased TBM penetration rates.
3: Your Crew is the Key
Knowledgeable operators are key in hard rock: there needs to be a balance between cutterhead speed and thrust force. An experienced TBM Operator will be able to identify when ground conditions change and react accordingly. In addition, knowledgeable operators know how to react if varying rock strengths are present in the excavation face. The most effective way to prevent impact loading in such conditions is to reduce cutterhead speed and penetration rate per revolution.
Maintenance is another key point and is especially important for extremely hard rock conditions. At the start of a project it is recommended to set a maintenance period for each day, say four hours out of each 24-hour period, which enables the crews to become familiar with the maintenance regime. This equates to approximately 24 hours of maintenance in a 6-day working week. Cutter change time can take up substantially more than four hours per day in hard rock tunnels, so once the crews are familiar with the maintenance tasks they are best carried out concurrently with cutter change operations.
Cutterhead inspections should be carried out on a regular basis to enable worn, damaged or blocked cutters to be replaced as soon as possible. Boring with even one blocked cutter can result in a cascading type wipe-out, which will progress rapidly in a chain reaction effect through multiple cutters if not immediately recognized. In hard rock this can also result in damage to the cutterhead over the course of just a couple of boring strokes. The same applies to the inspection of the bucket lips—these should be performed regularly and the bucket lips kept in good condition.
The Takeaways
Overall, ensuring success in some of the most difficult rock in the world requires pre-planning with proper machine design, good cooperation by all parties involved, a knowledgeable crew, and dedicated maintenance. More than that, it also takes some experimentation on the part of the contractor or those overseeing the TBM operation. Contractors can look at different cutter types and test the parameters of TBM operation, do regular penetration tests, vary the RPM, and vary the thrust to see what gets the best cutter life and the best TBM performance. Taking the time to do such testing can make all the difference between a successful project and an unsuccessful one.
Lastly, new and innovative cutter designs and housing designs exist for extremely hard rock. Consider XHD cutter rings, cutter mountings with hardened replaceable seats, and other designs that may be in development or available for testing. Posted by Steve Smading | Aug 21, 2019 | Insights in Brief
For further information please visit - https://www.therobbinscompany.com/3-ways-to-bore-hard-rock/