A Robbins
Crossover (XRE) TBM measuring 9.26 m (30.4 ft) in diameter underwent factory
acceptance on May 30, 2017. The gargantuan machine was initially unveiled at
Robbins’ Solon, Ohio headquarters during a press day on May 25 before being
shipped 40 km (25 mi) south for construction of the Ohio Canal Interceptor
Tunnel (OCIT) in Akron. Those present included Akron Mayor Daniel Horrigan,
Robbins chief engineer Dennis Ofiara, and David Chastka, project engineer for
contractor Kenny-Obayashi JV.
The TBM,
which includes features of both EPB and Hard Rock Single Shield TBM types, is
the first Crossover machine to be used in the United States. It will be
launched from a 12 m (40 ft) deep portal site and build the first 68 m (226 ft)
in soft ground, transitioning to a 183 m (600 ft) long zone of partial face
shale before switching to hard-rock mode for the remainder of the drive in full
face shale. Probe drilling will be done continuously using two probe drills to
determine which mode the TBM should be in.
Unique
aspects of the machine include a versatile cutterhead that will be configured
with consideration for both the short soft ground section and the longer
section (about 65% of the tunnel) in hard rock. A combination of disc cutters
and sacrificial rippers will be used in case a cutter becomes blocked.
The required rolling torque of the disc cutters has been reduced by 25% to
encourage smooth rotation in soft ground. The motors of the XRE machine have
been reworked from an original EPB configuration to permit higher motor speed
at reduced torque for the open mode segments of the drive.
Muck removal
will be achieved with a durable screw conveyor, the first flight of which is
covered welded-in wear plates. The auger shaft is lined with hard facing in a
crosshatch pattern, while the screw conveyor casing has been similarly lined in
wear plates and hard facing. A wear monitoring plan has been prepared for
the entire drive in order to maximize efficiency in the section of more
abrasive rock. Robbins Project Manager Pablo Salazar is proud of the
utilization of local jobs during the TBM construction and design process: “We
have built good portion of the machine in the northeast Ohio area. Many
components were fabricated locally with sub-suppliers, as well as in our own
shop.” The muck will be transported out of the tunnel using a Robbins
continuous conveyor system—the setup will be the 100th such conveyor supplied
by Robbins for operation behind a TBM.
The machine
was dubbed “Rosie” in honor of Rosie the Riveter, an icon representing the
American women who worked in factories and shipyards during World War II.
Hundreds of “Rosies” including Akron resident Rose May Jacob worked in
factories to turn out materials and armaments for the Allied war effort. The
TBM will be shipped in truckloads to the jobsite, with the large cutterhead
shipped in four pieces. “The entire process of assembly has allowed the
contractor to follow very closely through the testing of the machine, so they
are very familiar with the TBM at this point. At the jobsite, we will also
provide immediate support for both spare parts and personnel,” said Salazar.
Jobsite supervisors from Robbins will assist in TBM assembly and excavation for
at least the first 1,000 m (3,280 ft) of boring. Tunnel boring is
scheduled to begin in August of this year.
The OCIT
Project for the City of Akron consists of the construction of a conveyance and
storage tunnel system to control Combined Sewer Overflows (CSOs) for several
regulators in the downtown Akron area. The EPA-mandated project includes the
1.89 km (1.17 mi) conveyance and storage tunnel, as well as drop shafts,
diversion structures, consolidation sewers, and related structures. The
consent decree specifies that the tunnel must be operational by December 31,
2018. For further information visit http://www.therobbinscompany.com/.26/17.
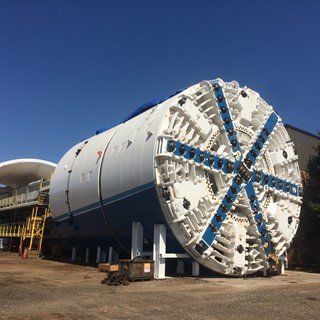