Underground construction is high risk; the extensive length
and size of a tunnel build through unknown rock strata poses the continual
threat of fire or rock fall. To manage this risk effectively, it is imperative
there are safety measures in place to protect all personnel on site. An
important, and often misunderstood safety resource is refuge chambers.
What Are Tunnelling Refuge Chambers?
Refuge chambers are sealed environments, built to sustain
life during an emergency or hazardous situation. The chambers maintain a
habitable environment, where personnel can remain comfortably until rescued or
the hazard subsides.
The principles of life support focus on controlling the
following:
• Sealed
Environment: A secure, sealed internal volume, positively pressurised, to
ensure contaminants are unable to enter the occupied space.
• Breathable
Air: Respirable air with multiple redundancies; required within a closed
circuit breathing apparatus that is the refuge chamber.
• Habitable
Environment: Temperature and humidity.
• Stand-alone
Mode: Electrical redundancy, with the use of a significant 24-hour
uninterruptable power supply, to operate scrubbing equipment, air conditioners,
lighting and gas monitoring equipment.
MineARC Systems have been designing and manufacturing refuge
chambers for the mining, tunnelling and petrochemical industries for 20 years.
As members of the International Tunnelling and Underground Space Association
(ITA), MineARC have engineered a series of refuge chambers and safety solutions
recognised at the forefront of the industry. MineARC’s range of TunnelSAFE
Refuge Chambers offers a solution for every application and requirement; from
Tunnel Boring Machine (TBM) gantry-mounted designs, to mobile rail models, to
transportable drill and blast units.
Developing refuge chambers for a tunnelling emergency
presents unique problems as there are specific needs of the industry and
conditions of each project. Some of the challenges MineARC engineers face
during the design process include:
Challenge: Respirable Atmosphere
Externally, compressed air is usually the primary source for
respirable air within a refuge chamber. MineARC’s engineers explored the
operational patterns of underground compressors as a primary breathing air
supply, the risks posed by the supply of potentially polluted compressed air
both during occupied and non-occupied scenarios, and methods to remotely
monitor and control the contaminated air from entering the sealed space. An
underground fire is one of the main causes of contaminated air, and reasons to
evacuate to a refuge chamber. As such, considerations around oxygen deprived,
high carbon monoxide and high-temperature air were used to begin the design
work for this life-support system.
Solution: Compressed Air Management System (CAMS)
A key feature of TunnelSAFE Refuge Chamber is the Compressed
Air Management System (CAMS); designed explicitly around the challenge of
maintaining a respirable atmosphere within an enclosed space. An oxygen sensor
is used to monitor incoming compressed air and will auto-close a solenoid in
the event of low oxygen. Air that is sourced from an area experiencing a fire
or from an environment that is likely to contain carbon monoxide as a result of
incomplete combustion will also have reduced levels of oxygen. This air
management system allows the internal volume of a refuge chamber to remain
respirable with or without occupants.
Challenge: Temperature and Humidity
In tunnelling applications, high ambient conditions for
conventional air conditioning units are often considered. Most common air
conditioning heat exchangers will be unable to reject heat higher than an
ambient temperature of 47°C. “High temperature” air conditioners are often
rated to 60°C but will have a more significant power draw and lower effective
cooling capacity.
Solution: Computational Fluid Dynamics (CFD)
MineARC has existing high temperature and insulated designs
that incorporate Computational Fluid Dynamics (CFD) modelling and analysis to
ensure occupant safety.
A baseline must first be established to identify if air
conditioning or insulation is required.
Metabolic heat output is quantified as 117W, though 130W is used in
these conditions. In Figure 1.0 below, it is clear that the chamber is already
reaching uninhabitable environmental conditions within the first 30 minutes of
entrapment. If the chamber detailed in Figure 1.0 were to reach saturation, the
heat index would exceed survivable limits within 30 minutes.
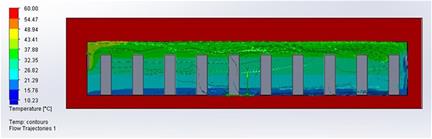
Figure 1:
Cross section: Scenario: Air Conditioning – No Insulation
Figure 2.0 and Figure 3.0: Computed with our standard
operating conditions, show the significant mixing ability by drawing in
contaminated air through chemical scrubbing cartridges. Though this scenario
does not consider the high ambient temperatures, it does add weight to the
mixing and cooling ability of a standard chamber in high-temperature
conditions.
Figure
2: Cross section - Standard Temperature Scenario:
Air
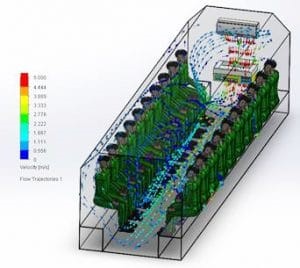
Figure 3: ISO2
- Standard Temperature Scenario: Air Conditioning – Scrubbing Fan Mixture
Designing the Future of Safety
Safety systems need to go beyond basic protection, to provide a complete management solution; monitoring operations, evaluating faults and giving immediate alerts. Having an integrated safety network that provides real-time communications and reporting can increase the effectiveness of safety and emergency response teams in the event of an emergency –ultimately saving lives.
Greater technology means better documentation which in turn allows for the recording and analysis of data from multiple assets with most systems transferring information in real-time.
In terms of safety, management of personnel coupled with improved data monitoring and assessment has a positive impact upon risk. Data allows for the identification and evaluation of hazards, which allows for the ability to control and mitigate associated risk; facilitating continual improvement. For technology to improve safety on a tunnelling project, it needs to address the following:
• Automation: Often menial and time-consuming tasks are mechanised to streamline processes and create a competitive advantage. Collating data from a number of sources over time offers a unique insight into geographical movements, equipment life cycles and liabilities.
• Integration: Plug-and-play systems, such as MineARC’s GuardIAN Intelligence Network, are capable of integrating into various operating software, across multiple industries.
• Behaviour: Technology also has the ability to curb behaviour, lessening human error through improved operations, advancement in occupational health and safety as well as identifying training opportunities.
MineARC’s GuardIAN enables real-time monitoring of all vital refuge operating systems via an online interface that can be accessed from any computer, tablet or smartphone. GuardIAN integrates with many existing MineARC Refuge Chamber technologies including Aura-FX Gas Monitoring, the Compressed Air Management System (CAMS) and the Satellite UPS Battery Bank System to simplify maintenance requirements and provide the confidence that a site’s fleet of refuge chambers is emergency ready at all times.
The adoption of new technologies will overcome common problems many organisations deal with on a daily basis when it comes to safety planning. Streamlining operational procedures through connected assets and data transfer will improve safety and regulatory compliance, and provide peace of mind that personnel are accounted for at any given time
Safety is paramount in any tunnelling project. Safeguarding against accidents and emergencies requires you to supply your project with trusted tunnelling safety initiatives. Due to the nature of tunnelling and underground construction, proactive safety management and emergency response planning are critical to ensuring the health and well-being of workers above and below ground. Incorporating smart technology, with industry designed refuge chambers, will improve safety and operations – ultimately saving lives.
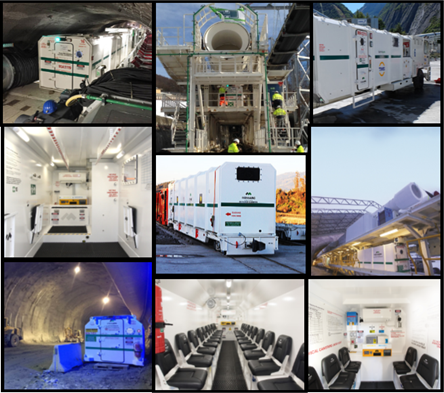
For further information on MineARC Systems Tunnelling safety
solutions visit minearc.com or contact the team at info@minearc.com.au